INTERVIEW WITH JULIAN GJERGJI,
HEAD OF POT AND LID LINE
WE HAVE RISEN TO THE CHALLENGES
SINCE WHEN HAVE YOU BEEN WORKING AT KUHN RIKON?
I have been employed at Kuhn Rikon since November 2017.
YOU ARE RESPONSIBLE FOR THE PRODUCTION OF THE NEW “NEW LIFE” FRYING PAN. WHAT DO YOU HAVE TO SEE TO HERE?
I see to the planning, provision of the materials and organising of the tests for this new development. I am also responsible for the coordination of the collaboration with the Technology department in the developmental phase and bringing into production, as well as for staff planning and capacity.
YOU ALSO HELPED DEVELOP THE NEW LIFE FRYING PAN. WHAT WERE THE CHALLENGES YOU FACED (AND HOW DID YOU SOLVE THE PROBLEMS)?
The material has different specifications and so we faced a big challenge in finding the right parameters for the machines. In general, aluminium behaves quite differently to chrome steel of course. The whole subject of reshaping and further processing had to be completely re-thought, and then had to be integrated into production together with tests. We spent many hours learning the correct influencing factors for the properties of aluminium and then realising this in the product. In this connection, we also had to test other processing materials and work closely together with our suppliers.
FOR THE FIRST TIME IN 35 YEARS, WE ARE ONCE AGAIN PRODUCING A FRYING PAN IN ALUMINIUM AT OUR SWISS PRODUCTION SITE. WHAT DOES THIS MEAN FOR PRODUCTION?
We are proud. Obviously, it was a re-adjustment for us but, nevertheless, we were all prepared to put this effort in, and work on the development and implementation. Our toolmaking workshop had to manufacture new tools for various processes. New/other material does however open up new possibilities as well of course, which can be used in future.
TOGETHER WITH THE HEAD OF QUALITY MANAGEMENT, YOU ARE RESPONSIBLE FOR LEAN MANAGEMENT. CAN YOU BRIEFLY EXPLAIN WHAT THIS INVOLVES?
The Swiss production site is one of the costliest in the world. Lean Management is to be understood as process improvement and optimisation. It is our job to make the staff and management aware of the topic “Lean” (lean processes) and train them. Each worker is to improve our processes through CIP (Continual Improvement Process) and thus optimise their own workstation. We are involving every single member of staff in this process as every staff member knows his own workstation best. Only the optimisation of work processes will bring continuing success in future.
WHAT IS YOUR FAVOURITE PRODUCT AND HOW COME?
My favourite product is the DUROMATIC® pressure cooker. As a firm believer in Lean J, I support optimised processes, and this is what the pressure cooker provides. For me, it embodies optimised and efficient cooking.
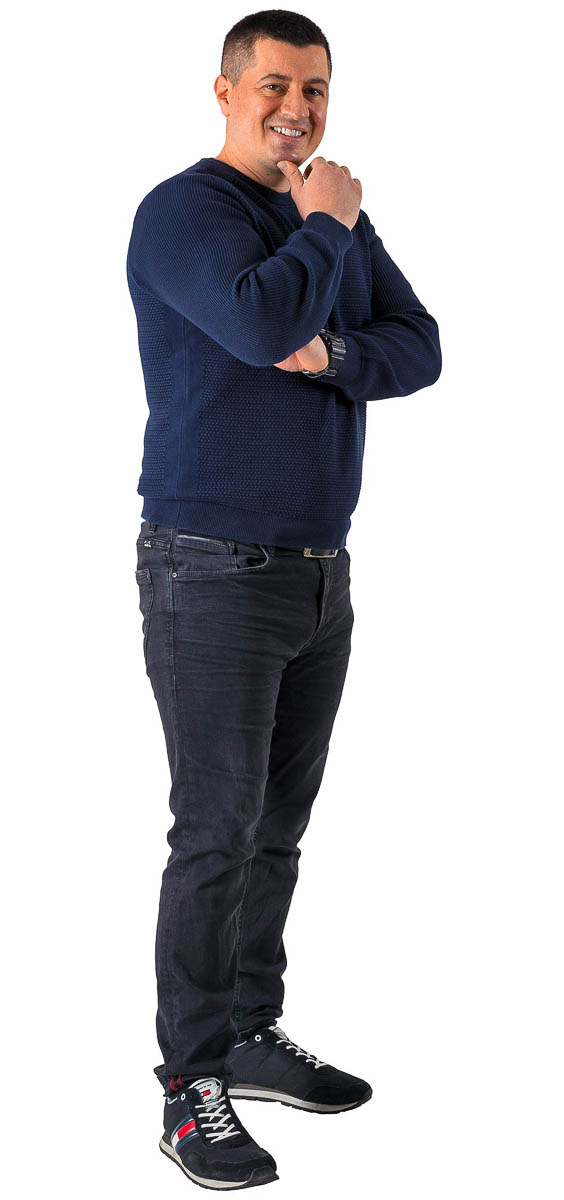
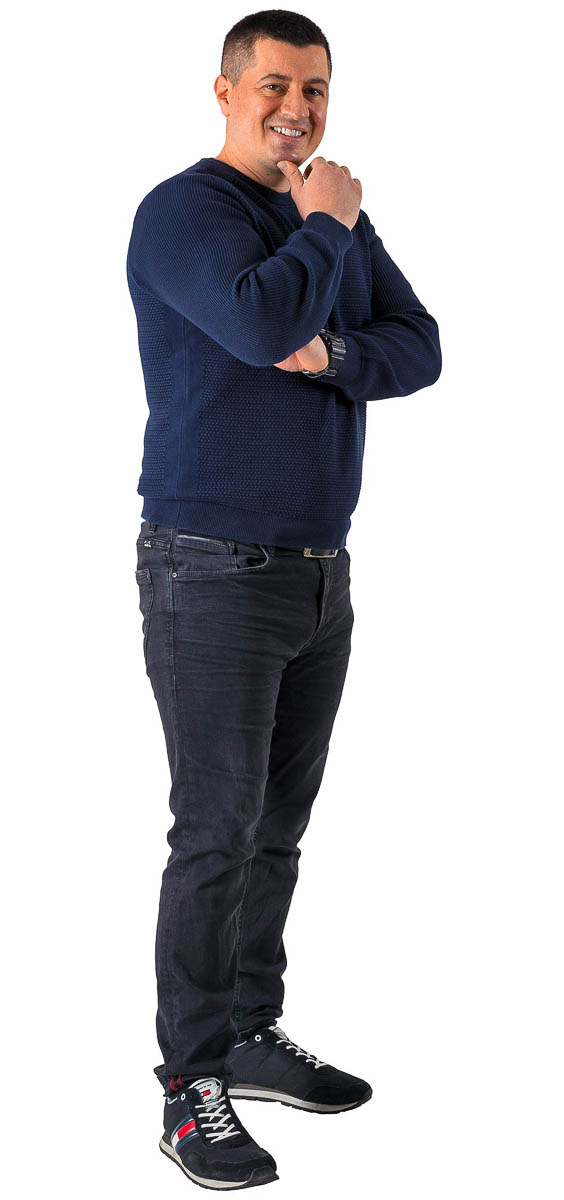